Decoding Electrical Failures: Unravelling the Essentials
As technology drives nearly every aspect of our daily lives, the reliability of electrical systems and devices is of paramount importance. From household appliances to industrial machinery and complex electronic devices, electrical systems are integral to modern living.
However, when these systems fail, the consequences can be significant, ranging from minor inconveniences to catastrophic events. Understanding the root causes of electrical failures and how to prevent them is essential for ensuring the safety, efficiency, and longevity of electrical systems.
Let’s delve into the essentials of electrical failure analysis, exploring the methodologies used to identify and address these failures while examining the critical role that third-party laboratories play in this field.
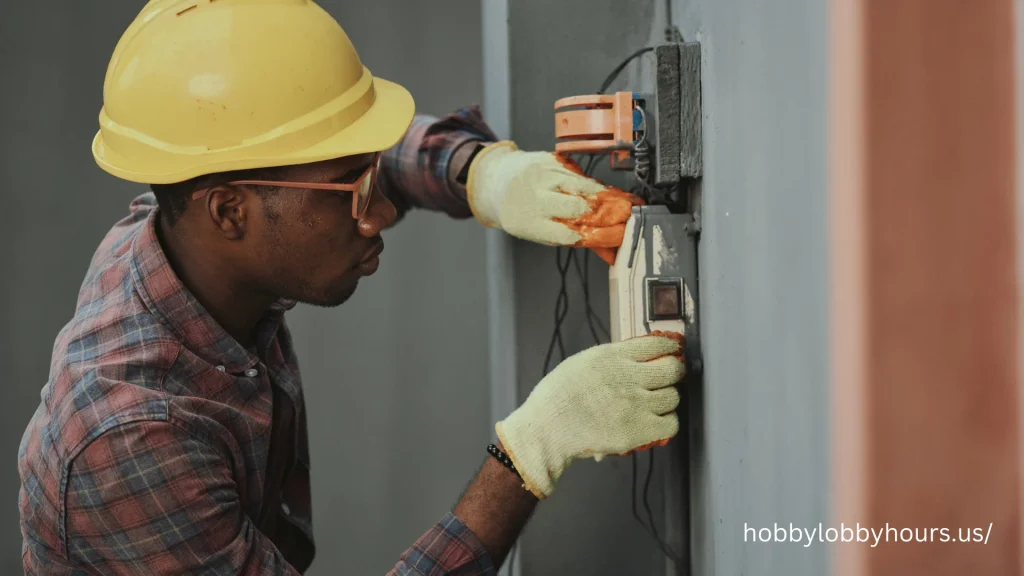
Understanding Electrical Failures
Electrical failures can occur in a wide variety of systems, from simple circuits to complex electronic devices. These failures are typically categorized based on their nature and cause:
- Component Failures: These occur when individual components within a system, such as resistors, capacitors, or transistors, fail due to manufacturing defects, material fatigue, or external stresses.
- Systemic Failures: These involve the entire system malfunctioning due to design flaws, improper installation, or external influences like power surges, environmental conditions, or electromagnetic interference.
- Intermittent Failures: These are sporadic and unpredictable, making them particularly challenging to diagnose. They may result from loose connections, fluctuating environmental conditions, or transient electrical disturbances.
- Catastrophic Failures: These are sudden and severe, often leading to complete system shutdowns or even physical damage, such as electrical fires or explosions.
Understanding the specific type of failure is the first step in the diagnostic process. However, to effectively prevent future occurrences, a deeper analysis is required to uncover the root causes.
The Process of Electrical Failure Analysis
Electrical failure analysis (EFA) is a systematic approach to identifying the underlying causes of electrical malfunctions. This process typically involves several key steps:
- Initial Assessment: The first step in EFA is to gather all relevant information about the failed system. This includes the system’s design specifications, manufacturing process, operational history, and any observed symptoms of failure. This data provides a foundation for the subsequent analysis.
- Non-Destructive Testing: Before any invasive procedures are conducted, non-destructive testing (NDT) techniques are employed to examine the system without causing further damage. Techniques such as X-ray imaging, infrared thermography, and scanning electron microscopy (SEM) allow analysts to detect internal defects, such as cracks, voids, or corrosion, without disassembling the device.
- Destructive Analysis: Once non-destructive methods have provided preliminary insights, destructive techniques may be used to delve deeper into the system. This can involve cross-sectioning components, decapsulation, or chemical analysis to reveal hidden defects or material weaknesses.
- Root Cause Analysis: After collecting data through testing, the next step is root cause analysis. This involves comparing the observed failure characteristics with known failure modes to identify the most likely cause. For example, a capacitor that fails due to overheating might indicate a design flaw in the thermal management of the system.
- Corrective Actions: The final step in EFA is to recommend corrective actions based on the findings. These recommendations might include design changes, material substitutions, or improved quality control processes to prevent similar failures in the future.
Also check: Understanding Connected TV Measurement Techniques
The Role of Leading Laboratories in Electrical Failure Analysis
When it comes to conducting detailed and accurate electrical failure analysis, the expertise and resources of specialized laboratories are invaluable. Wintech Nano, a leading third-party commercial laboratory in Singapore, is at the forefront of this field. With state-of-the-art facilities and a team of highly skilled experts, this laboratory provides comprehensive failure analysis services to a wide range of industries, including electronics, aerospace, automotive, and consumer goods.
Their approach to EFA is rooted in a deep understanding of the complexities of electrical systems and the various factors that can lead to failure. By combining advanced testing methodologies with rigorous analytical techniques, the laboratory delivers precise and reliable results that help manufacturers improve product quality, enhance safety, and reduce the risk of future failures.
For companies operating in highly competitive markets, the insights provided by this laboratory can be critical in maintaining a competitive edge. By identifying potential failure points early in the design or production process, manufacturers can implement preventive measures that not only improve product reliability but also enhance customer satisfaction and brand reputation.
The Importance of Electrical Failure Analysis in Industry
Electrical failure analysis is not just a diagnostic tool; it is a vital component of quality assurance and risk management in various industries. Here’s why EFA is essential:
- Improving Product Reliability: By identifying and addressing the root causes of electrical failures, manufacturers can enhance the reliability and durability of their products. This reduces the likelihood of product recalls, warranty claims, and negative customer experiences.
- Ensuring Safety: Electrical failures can pose significant safety risks, including electrical fires, shocks, and explosions. EFA helps identify and mitigate these risks, ensuring that products meet stringent safety standards.
- Reducing Downtime: In industrial settings, electrical failures can lead to costly downtime. By understanding the causes of these failures, companies can implement strategies to minimize disruptions and maintain continuous operations.
- Supporting Innovation: EFA provides valuable insights that drive innovation. By understanding how and why failures occur, engineers and designers can develop new solutions and technologies that push the boundaries of what is possible.
- Maintaining Compliance: Many industries are subject to strict regulatory requirements regarding product safety and performance. EFA helps ensure that products comply with these regulations, avoiding legal liabilities and fines.
Personal Perspectives and Insights
Having worked closely with professionals in the field of electrical failure analysis, I have developed a deep appreciation for the meticulousness and expertise required in this discipline. Electrical failures are often seen as mere technical issues, but they have broader implications that can affect safety, efficiency, and even the reputation of a brand.
One memorable experience involved a case where a critical industrial system failed unexpectedly, leading to significant operational disruptions. The initial assumption was that the failure was due to a manufacturing defect in a key component.
However, after a detailed failure analysis conducted by a third-party laboratory, it was discovered that the root cause was a subtle design flaw that had gone unnoticed during the initial development phase. The insights gained from the analysis not only resolved the immediate issue but also led to design improvements that enhanced the overall reliability of the system.
This experience underscored the importance of electrical failure analysis as more than just a reactive measure—it is a proactive tool that can drive continuous improvement and innovation. For organizations committed to excellence, investing in high-quality failure analysis services is not just a necessity but a strategic advantage.
Takeaways
- Electrical failure analysis is essential for identifying and addressing the root causes of electrical malfunctions and improving product reliability and safety.
- Non-destructive and destructive testing methods are integral to the failure analysis process, providing insights without causing additional damage to the system.
- Leading third-party commercial laboratories in Singapore offer advanced failure analysis services that help manufacturers enhance product quality and reduce risk.
- Electrical failure analysis is critical in ensuring compliance with safety and performance standards, reducing the likelihood of costly recalls and legal liabilities.
- Investing in failure analysis not only resolves current issues but also drives innovation and continuous improvement, providing a competitive edge in the market.
Electrical failure analysis is a vital discipline that plays a crucial role in ensuring the reliability, safety, and efficiency of electrical systems across various industries. By partnering with experts, organizations can gain valuable insights that not only address immediate concerns but also contribute to long-term success and innovation.